Coley Park High Rise RIBA Stage 3 Fire Safety Strategy
OFR Consultants retrospective fire safety strategy for the refurbishment of the Coley Park High Rise residential blocks.
Contents
- Introduction
- Appointment
- This report
- Legislative requirements
- Basis of design
- Amended regulations and guidance regarding external wall construction
- Construction phase of works
- Development overview
- Development overview
- Summary
- Items to be confirmed to OFR
- B1 – Means of warning and escape
- Evacuation strategy
- Evacuation of mobility impaired persons (MIP)
- Horizontal egress
- Apartments
- Common residential corridors
- Residential ancillary areas
- Vertical egress
- Escape stair
- Smoke control
- Stair discharge
- Protection of final exits
- Active fire safety systems
- Means of warning
- Residential accommodation
- Residential sprinkler system
- Smoke ventilation systems
- Refuse store
- Residential common corridor and stair
- Ground floor fire-fighting lobby
- Emergency lighting
- Fire safety signage
- Emergency power supplies
- Means of warning
- B2 – Internal fire spread (linings)
- B3 – Internal fire spread (structure)
- Structural fire protection
- Compartmentation
- Fire doors
- Concealed spaces
- Cavity barriers
- Fire-stopping at junctions
- Fire-stopping around services
- Pipes
- Ductwork
- B4 – External fire spread
- External wall construction
- Roof coverings
- Space separation calculations
- Access and facilities for the fire service
- Vehicle access
- Firefighting shaft
- Dry rising main
- Hydrants
- Wayfinding signage
- Management requirements
Appendix A: to be developed – Draft fire strategy drawings
1 Introduction
1.1 Appointment
OFR Consultants (OFR) have been appointed by Reading Borough Council to provide fire safety advice for the proposed refurbishment of the existing high rise residential developments known as Coley Park High Rise located on Wensley Road in Reading. There are 3 blocks 193, 203, & 205 Wensley Road.
The buildings are existing residential blocks of flats constructed circa 1960, the blocks do not currently have a fire safety strategy, remedial/refurbishment works are to be carried out to the blocks and OFR have been requested to develop a retrospective fire strategy covering the existing building layouts and the proposed improvements.
(Note: OFR have been informed by comment on the retrospective strategy that RBC do have an existing building strategy for the blocks which sets out a ‘stay put’ policy for evacuation, contains PEEPs, details of the common AFD and sprinkler systems and engagement/education of the tenants – at the time of the draft and revision of this strategy OFR had not been in receipt of this document).
This report has used the layouts relating to Block 193, however the layout of blocks 203 & 205 Wensley Road are considered to have the same generic layout.
The purpose of this report is to document the existing fire strategy for the building and provide a comparison to current guidance etc. Where aspects of the existing fire strategy are understood not to follow current guidance, recommendations have been provided. All recommendations should be considered by the Fire Risk Assessor and Responsible person, prior to implementing any remedial works. It is noted that this is an existing building, and it is likely that the design and layout would have been based on guidance applicable at the time.
It is thought that at the time of construction, the relevant guidance would have been CP 3 Chapter IV Part 1, Code of Basic data for the design of buildings Chapter IV Precautions against fire Part 1 Flats and Maisonettes (in blocks over 2 storeys) and would appear to tie up with the general layouts of the blocks, it is understood that RBC do not hold existing records to be able to confirm this, but their acceptance of the of the OFR assumption for the design guide of construction is requested.
At the time of writing of this report the only available revision of this document available to OFR was 1962 as amended. This document has been used as the basis of review of the existing building.
It should be noted that where there is reference to the existing layouts of the building and guidance, this does not constitute OFR’s support/agreement to the fire safety facilities within.
1.2 This Report
This report is based primarily on the drawing information produced by HTA Architects, as listed in Table 1. as well as the latest Fire Risk assessment for the blocks dated 26/02/2019 Reference B9791.
The aim of this report is to inform the client and design team of the of possible legislative requirements, design challenges, and proposed solutions that they need to be aware of as the project progresses. These include elements of the fire safety design that present a variation from standard and current guidance. This report is intended to document the strategic fire safety design approach to be adopted rather than provide detailed construction and specification information.
There will be elements within the buildings that are existing and not planned to be changed by RBC as part of the refurbishment and where this is the case, the responsibility for the element, that is the design, install, management and implementation lies with RBC.
Title | Drawing number | Revision | Drawing Date |
---|---|---|---|
Proposed Level 00 | RBC-CRR_HTA-A_DR_193_2000 | Preliminary First issue | 15/10/2021 |
Proposed Upper Levels Plan 1 of 2 | RBC-CRR_HTA-A_DR_193_2001 | Preliminary First issue | 15/10/2021 |
Proposed Upper Levels Plan 2 of 2 | RBC-CRR_HTA-A_DR_193_2002 | Preliminary First issue | 15/10/2021 |
Proposed GA Plan – Level 02 | RBC-CRR_HTA-A_DR_193_2003 | Preliminary First issue | 15/10/2021 |
Proposed GA Plan – Level 03 | RBC-CRR_HTA-A_DR_193_2100 | Preliminary First issue | 15/10/2021 |
Proposed GA Plan – Level 04 | RBC-CRR_HTA-A_DR_193_2101 | Preliminary First issue | 15/10/2021 |
Proposed GA Plan – Level 05 | RBC-CRR_HTA-A_DR_193_2102 | Preliminary First issue | 15/10/2021 |
Section A-A | RBC-CRR_HTA-A_DR_193_2200 | Preliminary First issue | 15/10/2021 |
Section B-B | RBC-CRR_HTA-A_DR_193_2201 | Preliminary First issue | 15/10/2021 |
1.3 Legislative requirements
For new developments Fire safety of building works is legislated by the Building Regulations 2010 (including amendments) “the Regulations”. The Regulations have been enacted under the Building Act 1984 and are published by the Controller of HMSO (Her Majesty’s Stationary Office). The Regulations impose requirements on people carrying out building work. The requirements are functional rather than prescriptive in nature, meaning that the designer is given the freedom to choose the method they use to satisfy the legislation.
The strategy has been developed to address the requirements of Part B of the Regulations, that governs fire safety of building design. These requirements are segregated into the following distinct aspects of building design:
- B1 – Means of warning and escape;
- B2 – Internal fire spread (linings);
- B3 – Internal fire spread (structure);
- B4 – External fire spread; and
- B5 – Access and facilities for the fire service.
At the appropriate stage, the report should be forwarded to the building owner and / or operator, under Regulation 38 to assist the responsible person to operate and maintain the building with reasonable safety in accordance with the Regulatory Reform (Fire Safety) Order 2015 (RRO). This will also be used inform their fire risk assessments, which will need to be prepared by the relevant Responsible Person prior to operating the building (typically the building owner / management team) under the RRO following the completion of any alteration/remedial works
The strategy has been developed in cognisance of the Construction (Design and Management) Regulations 2015 (CDM 2015), which sets out what designers are required to consider in order to protect anyone involved in the construction or ongoing use of a project. The strategy does not address site fire safety during the building works.
The Health and Safety Executive (HSE) issues guidance notes on identifying and managing fire precautions during the works and they should be consulted by the appropriate party.
Where works are to be carried out to existing buildings it may also be necessary to refer to legislation and guidance applicable at the time of the construction (as previously noted) and any significant alterations that may have been carried out in the life of the buildings – this should be reviewed in line with the latest building fire risk assessment carried out under the Regulatory Reform Fire Safety order 2005, (RRO).
1.4 Basis of Design
The purpose of this retrospective fire strategy is to review the fire safety features within the existing building against guidance at the time of construction and provide a comparison with current guidance, Approved Document B Part 1 2019. Where aspects of the existing fire strategy are understood not to follow current guidance, recommendations have been provided. It is recognised that the buildings to which this strategy refer to are existing structures and it may not be reasonably practicable to bring the features within to the level of current standards and therefore the recommendations within this report these should be passed to the Fire Risk assessor and Responsible Person for consideration.
As detailed in the introduction it is noted that this is an existing building and it is likely that the design and layout would have been based on guidance applicable at the time which is thought to be CP 3 Chapter IV Part 1, Code of Basic data for the design of buildings Chapter IV Precautions against fire Part 1 Flats and Maisonettes (in blocks over 2 storeys). At the time of writing of this report the only available revision of this document available to the writer was 1962 as amended and has been used as the basis of this retrospective strategy. This document has been used as the basis of review of the existing building.
The current design guidance the building has been reviewed against is the AD B 2019 Part 1 for the residential areas.
This report highlights aspects in relation to current design guidance. Where this is the case reference should also be made to the details in Regulation 3 and Regulation 4 of the Building Regulations in relation to ‘material alteration’ and ‘building work’ and in particular to Regulation 4(3) which requires that once building work has been completed, the building as a whole must comply with the relevant requirements of Schedule 1 (of the Building Regulations), or, where it did not comply before, must be made no more unsatisfactory than it was before the work was carried out. The recommendation is that the nominated Building Control approval body provides detailed advice/comment, on what is considered to be appropriate in respect of the above.
However, this strategy report should be made available to the responsible person as part of the preparation of the building Fire Risk Assessment and reviewed along with the facilities within the existing building to formulate the risk assessment under the RR(FS)O 2005.
All aspects of the fire safety design remain subject to review by the building control body (including their statutory consultation with the local fire and rescue service), and, ultimately, formal approval by the Building Control Body.
1.5 Amended Regulations and Guidance Regarding External Wall Construction
As of the December 2018, the amendment to the Building Regulations 2010 and the associated changes to the Approved Document B (Fire Safety) and Regulation 7 (Workmanship and Materials) came into effect.
Regulation 7 has been amended to require that, in relevant buildings (primarily those having areas of sleeping risk), materials which are part of or within an external wall and specified attachments must achieve European Class A2-s1, d0 or Class A1 when classified in accordance with BS EN 13501-1. As this is part of The Regulations, this is prescriptive and alternative routes to compliance are not available.
The definition of external wall has been extended to include all items from the warm internal face to the cold/wet external surface and the addition of a new category titled “specified attachment” which includes items like balconies. There are specific exceptions to the requirements (such as window frames, glazing and doors), thermal breaks and minor items like seals and gaskets. Other than the excepted items, detailed in Regulation 7(3), the new regulation is intended to be all encompassing, and the pretermission of appropriately classified products based upon technicalities is considered to be outside of the intent of The Regulations.
A separate review of the proposed external wall materials is to be carried out prior to installation on site and can be added as an addendum to this strategy
1.6 Construction phase of the works
This strategy mainly relates to the works when completed and does not fully cover the construction stages, it is understood that the blocks will remain occupied during the duration of the programme of work and it will be the responsibility of the nominated contractor to ensure the safety of the residents at all times.
This strategy should be used as a basis for the life safety measures required and should be used to prepare the construction site fire safety strategy and by the nominated contractor as required by the HSE executive, using guidance such as HSG 168, Fire Safety in Construction or the latest revision of the FPA Construction Site Fire safety.
It is paramount that the life safety provisions within the buildings are maintained at all times, safety routes should be kept clear and fire-fighting access and provisions maintained.
It is likely that the construction site fire safety plan will need revision as the work progresses.
2 Development Overview
2.1 Development Overview
The Coley Park High Rise development consists of three existing residential blocks, 193/ 203/ 205. Each with 15 floors above the ground floor access level (16 floors in total). The blocks do not have a basement level. It is understood that the blocks were constructed circa 1960. OFR have been notified that the blocks have been constructed in Wimpey ‘no-fines’ concrete construction. Note the term No fines” relates to the name of the type of concrete that was used in the construction of this system of house building. No-Fines concrete is a non- proprietary material used widely in England and Scotland for the construction of walls in dwellings. It comprises of a mix of concrete that contains no sand or other small particles of very fine gravel, collectively known as ‘no- fines’.
Often the mix used contains 3/4″ or 1/2″ sizes stones or gravel as the sole aggregate constituent. This mix creates a honeycomb structure within the concrete leading to a product with a higher insulation value (lower U-value) when compared to standard dense concrete. The approximate height of the topmost occupied floor is 38.5m (to be confirmed). The blocks have communal space at the ground floor access level, in the form of refuse stores and additional communal facilities on each of the residential floors accessed from the communal corridor, refuse chutes and communal drying rooms.
There are 2 stairs that provide escape from all floors, there are 2 lifts that provide access to alternate floors – one for odds and the other evens, bot lifts are provided with fire service override switches.
The blocks have recently had a sprinkler system installed which OFR have been advised by RBC to be in accordance with the guidance in BS 9251: 2014, a detailed review of this has not been carried out by OFR. The blocks are each provided with a dry rising main serving all floors, the dry rising main inlet is located within the building, within the main communal entrance. There is an outlet for the main located centrally within the residential common corridor on each floor. It is understood that the current flat layout incorporates a protected hallway from the communal common corridor leading to the accommodation within each flat. OFR have been advised that the flats have an existing fire alarm and detection system which is understood to be to BS 5839: part 6 (to be confirmed). Detection within the ancillary areas is also to be confirmed by RBC.
It is understood that circa 1990 the block underwent refurbishment which included the improvement of thermal performance of the building and a STO external insulated render system was applied to the external façade, the insulation within the system is understood to have been a ‘fire retardant’ Expanded polystyrene, (EPS) and has been confirmed by RBC and HTA architects, although OFR had not reviewed specific details at the time of the revision of this report.
It has been proposed by RBC that works should be carried out to remove the existing rendered external insulation system and replace with a system that is non-combustible and compliant with current guidance in AD B 2019, at the same time the blocks will undergo internal refurbishment and minor alteration to the communal entrance at ground floor level and reconfigure the communal refuse stores as well as providing protection/enclosures at the base of the stairs. On the upper floors RBC are proposing to replace the existing bin chutes within the enclosures.
It is recommended to discuss this fire strategy with the Approving Authorities as early as possible and consult the Royal Berkshire Fire and Rescue Service, (RBFRS), before full remedial proposals are finalised. It is understood that at the time of writing this report that the Building Control function will be carried out by Reading Borough Council Building Control.
It is understood that there has been correspondence from the RBFRS relating to concerns within the residential blocks, prior to the planned works, but at the time of writing this draft strategy report OFR have not been provided with copies of any of the correspondence or notices.
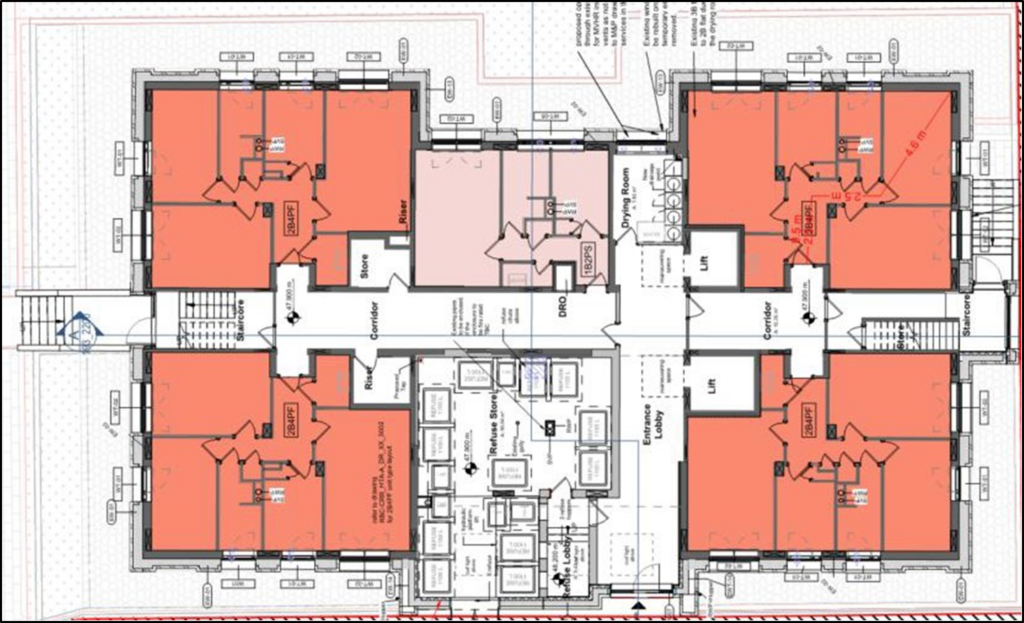
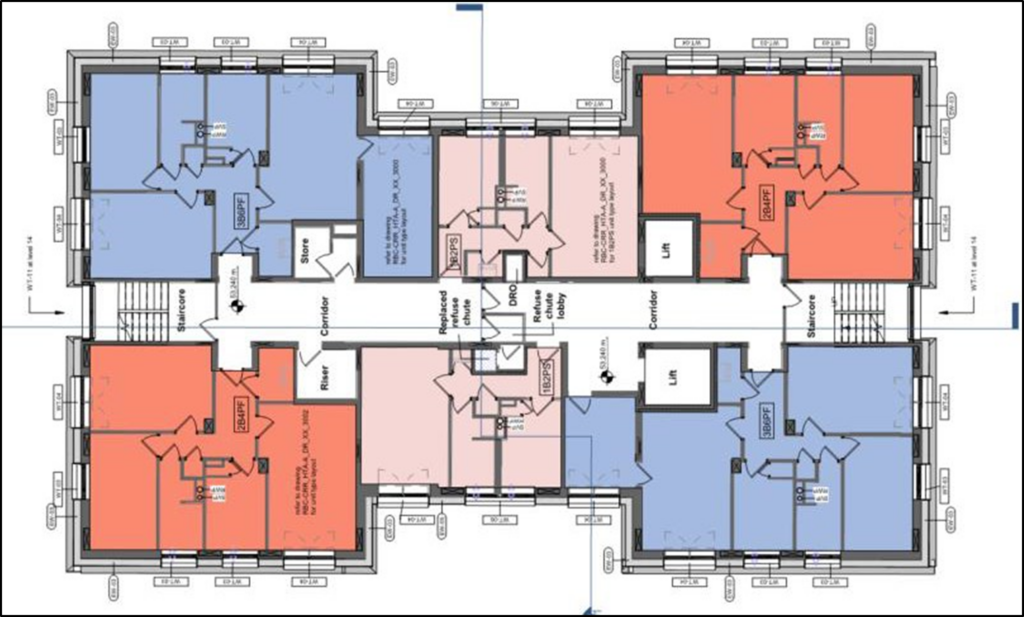
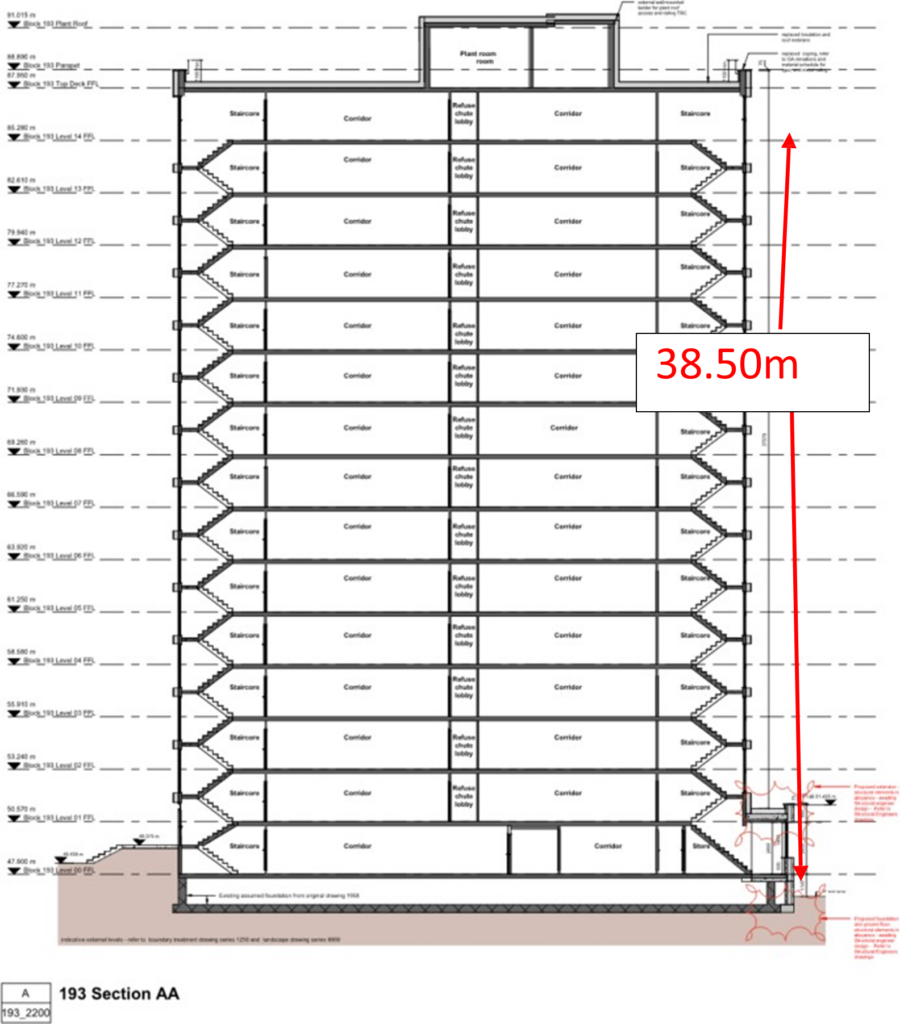
3 Summary
Table 2 below summarises some of the main elements of fire safety strategy for the blocks but should not be considered comprehensive or read in isolation of the main report. The areas highlighted require further clarification.
Item | Guidance at time of construction | Existing Measure Measures | Current Guidance | Proposed Measures |
---|---|---|---|---|
Height of top occupied floor level | – | c. 38.5m | – | n/a |
Guidance document | CP 3 Chapter IV Part 1 1960* | – | AD B part 1 2019 | Approved Document B 2019 where possible |
Suppression | n/a | BS 9251:2014 Install covers flats, communal areas, refuse storage and drying rooms. RBC to ensure design & commissioning details readily available for maintainer and for FRA review | BS9251: latest revision | Existing system to be retained |
Fire alarm and detection | n/a | BS 5839-6:2019 LD3 Grade D1 in flats confirmed by RBC; BS 5839-1:2017 system and level of system in all ancillary areas, common corridors and stairs to be confirmed by RBC. This will include C&E to ensure that there is no conflict with the residents ‘stay put evacuation’ strategy | BS 5839-6: 2019 LD2 Grade D1 in flats BS 5839-1: 2017 – L1 in all ancillary areas. BS 5839-1 2017 L5 in common areas to activate smoke control where fitted. | Detection in flats to remain as existing ie. BS 5839-6 LD3 detection. BS 5839-1:2017 L1 in common corridors and stair to activate smoke ventilation where installed – note these will be interfaced with the common alarm system noted below. BS 5839-1: 2017 L1 system in ancillary areas, common corridors and has been confirmed by RBC, with C&E and is to be retained. The system is existing and is not to be changed. It is important that RBC communicate clearly to residents the actions to be taken in the event of a fire emergency in their apartments or when notified of an activation in the common areas. Thie should also be communicated to the responsible person for the building FRA’s under the RRO, as well as the local fire service. |
Emergency Lighting (common areas) | Power supply by ‘protected circuits’ | Emergency lighting present with self-contained battery – Confirmed by RBC as EN 60598-2: 2020. | BS 5266-1: 2016 | To be retained as existing |
Travel distance in common area (corridor) | Not more than 15ft (4.6m) from flat entrance door to cross corridor smoke stop door or door to stair. | As per guidance in CP3 | 7.5m single direction, 30m in more than one direction* (excluding possible extension due to sprinkler protection. | To be retained |
Linings (Internal fire spread) | To be confirmed by RBC as couldn’t be established on site visit | Class 0 National Class; B-s3, d2 European Class | TBC as to whether surface treatments have been applied post completion | |
Staircase smoke ventilation | 15ft2 (1.4m2) ventilation provided at high level to each landing level. | Permanent vent less than 0.65m2 low level & high level in each stair. | AD B part 1 2019 | 1.25m2 ventilation provided at high level to each landing level. The vents to be located within the external wall of each stair core, to provide maximum practicable safe ventilation to stair core to level of existing building and with consideration to the as built non-ventilated corridors. The vents have been agreed in principle by the RBC building control to be AOV for the top and bottom vent and for the remainder to be manual opening by the fire service on attendance. |
Smoke ventilation (common residential corridors) | n/a | none | AD B part 1 2019 | To be retained as existing |
Smoke ventilation (other common areas) | n/a | No ventilation to the residential common corridors, existing situation, level of separation between apartments and corridor and cross corridor door to be confirmed. | Refuse store 0.4m2 permanent ventilation Ventilation to common corridor to be considered by design team and RBC, but likely to not be practicable to install. Level of separation between flats/ancillary accommodation and common corridor/stairs to be confirmed. | |
Evacuation Lift | n/a | Tbc | Not current in AD B 2019, but identified in London Plan Evacuation lift Note that is not applicable to Berkshire but is currently becoming common place in developments in London and is seen in a lot of instances to be ‘best practice’. | RBC still to confirm whether upgrade of existing lifts is practicable and this will be captured in any updated FRA’s for the blocks. This will need to be reviewed by the RBC Building Control and the RBFRS in consultation. |
Structural fire resistance | Assumed to be 120minutes – but specific guidance/requirements not known at time of construction | 120 min FR assumed Note: OFR has not carried out intrusive inspection of the structure. OFR understand that RBC has previously appointed a specialist structural survey of the buildings. OFR request that indicative FR performance of the existing structure is requested from the structural engineers. if | 120 mins | As existing. Recommendation that structural review identifies the likely structural fire resistance for the blocks. |
Firefighting shafts | No fire-fighting shaft – when assessed under current guidance, clarification as to whether lifts within the buildings are suitable for fire-fighting access and if required evacuation and how these will be managed. | As existing and confirmation from Fire service that in agreement for operational access | ||
Fire mains | Dry rising main – external inlet and outlets in corridors ‘as close as possible to stair of Fire service lift’. | Dry Rising Main, accessed internally – original inlet located in the ground outside main entrance of blocks | BS 9990. | As existing – current layout to be agreed by BC approval body and fire service in consultation |
Back-up power | Separate supply to serve lifts where FF access/use required. | Confirm the existing power supplies to the lifts. Original guidance suggests that this would be a separate feed to the reminder of the building to protect the supply in the event of building failure. | Detail existing and any proposed changes. |
4 Items to be confirmed to OFR
The table below summarises the points that need to be agreed with the Approving Authorities. Note that there are areas that need to be accepted and could be subject to change/addition items as the project develops.
Topic | Comments | Section |
---|---|---|
AFD to common Corridor and stairs | The AFD system in common areas would appear to be provided with sounders and would appear to contradict the stay put evacuation policy for blocks of flats – the cause and effects for the system should be reviewed | Section 6.1 |
Back-up power supply | Details of back-up power supply to allow lifts to be used in the event of fire emergency. | |
Fire Fighting Lift | Clarification is required as to whether existing lifts are suitable for FF access/use. These would have been required at the time of construction | Section 10.2 |
Fire-fighting shaft | No fire-fighting shaft – when assessed under current guidance, clarification as to whether lifts within the buildings are suitable for fire-fighting access and if required evacuation and how these will be managed. | Section 5.4, 10.3 |
Dry Rising Main inlet | Inlet for dry-rising main is located within the building within the residential lobby, this is not in line with current guidance or the understood guidance at the time of construction – it is to be confirmed that this is acceptable to the Building Control approval body and the Royal Berkshire Fire and rescue service. | Section 10.3 |
Ventilation (common corridor) | Non – provision of common corridor ventilation to be confirmed | Section 5.3 & 6.3 |
Ventilation (stairs) | Proposed 1.0m2 to each landing level within staircase – based on current guidance. (Current guidance would also require common corridor to be provided with smoke control system). The required ventilation at the time of construction would have been circa 1.4m2 at each landing level. | Section 5.3 & 6.3 |
5 B1 – Means of Warning and Escape
3.1 Evacuation Strategy
The existing evacuation strategy is understood to be ‘stay put’ as identified in the current Fire Risk Assessment, dated 26.06.2019. This evacuation strategy would be characterised as follows:
- Stand-alone detection and alarm systems within each residential apartment, with every apartment being evacuated independently – irrespective of a fire occurring in a neighbouring apartment, any other apartment within the building, any other residential plant and ancillary accommodation or non- residential accommodations. This approach does not preclude a resident’s ability to escape from their own free will should they wish to do so;
- Occupants may choose to evacuate themselves without Fire Service intervention and are freely able to do so;
- The evacuation of all other apartments will not generally take place unless instigated by the Fire Service.
This approach is commensurate with the accepted fire safety guidance for residential schemes and supported by the National Fire Chiefs Council, (NFCC).
The ancillary spaces at ground floor and on the upper floors are to operate a simultaneous evacuation strategy, where in the event of a fire in any of these spaces, all occupants in these spaces will evacuate at the same time. The residential flats should be safe to remain stay put. There would appear to be slight conflict in the ‘stay put’ evacuation strategy by the inclusion of a common alarm system within the common residential corridors and the stairs, the category of system installed should be confirmed as we as the cause and effects matrix for operation.
This should be reviewed as part of the building management and evacuation procedures and the responsible person as part of the building fire risk assessment under the RRO.
It is understood that all areas are provided with automatic fire detection and alarm in line with the guideline in BS 5839: Part 1 2017, the level of system is to be confirmed by RBC.. If not already provided it is recommended that the detection is linked back to a call receiving centre as the blocks do not have 24/7 management on site.
As there is detection and alarm in common areas consideration has been given by RBC to a suitable system cause and effects matrix for the system. Residents should be made aware of the actions to be taken in the event of a fire alarm activation and in particular where the existing residents building evacuation strategy is understood to be ‘stay put’.
It is important that the actions to be taken by residents for a fire in their flat and the activation of a detector/sounder in a common area of the building is carefully and clearly communicated to all of the residents by RBC and that RBC are in a position to manage any such situation.
The recommendation is that the fire evacuation procedures are also made clear to the responsible person under the RRO as well as the local fire service who may be in attendance in the event of a fire.
5.2 Evacuation of Mobility Impaired Persons (MIP)
The building currently does not have any refuge provisions for MIP and it is currently understood that the existing lifts are not suitable for the evacuation of mobility impaired persons. As the building operates a defend in place strategy, it is reasonable that evacuation lifts would not be required. However, the latest fire risk assessment (FRA) provided to OFR states the following:
“Although the property is not suitable for disabled persons with mobility issues, corridors are protected and could be used by disabled residents (currently in the building) as the next relative safe area in the event of a fire in their flats. This must be communicated to anyone that cannot use the stairs, and ensure PEEPS are carried out.”
OFR note that although the communal corridors are constructed to form compartments, there is no ventilation within the corridors, as such OFR would not class the communal corridors as a relative safe place area.
It would be beneficial for landlords to be notified of any changes of mobility of residents so that suitable precautions can be put in place to assist in evacuation however any such precautions may require management assistance.
5.3 Horizontal Egress
5.3.1 Apartments
The existing flat layout within the blocks incorporates an entrance hallway from the flat entrance door which then provides access to the internal rooms within the flat. It is understood that all internal flat walls are either concrete or masonry, the rating of the doors is to be confirmed allowing the flat hallways to be treated as a protected corridor. Information on the fire performance on the existing structure is to be confirmed by Calcinotto.
In the event that the travel from the furthest part within the residential flats to the flat entrance doors is more than 9m, the flats should be provided with a protected hallway, although there is mitigation in the event that the building has been fitted with a retrospective sprinkler system.
There are a number of flats within the central part of the blocks which have rooms which have 2 routes of escape, either through a residential access room or an alternative direct to the common corridor as shown in Figure 4 below, the inner rooms have a separate escape to the common residential corridor.
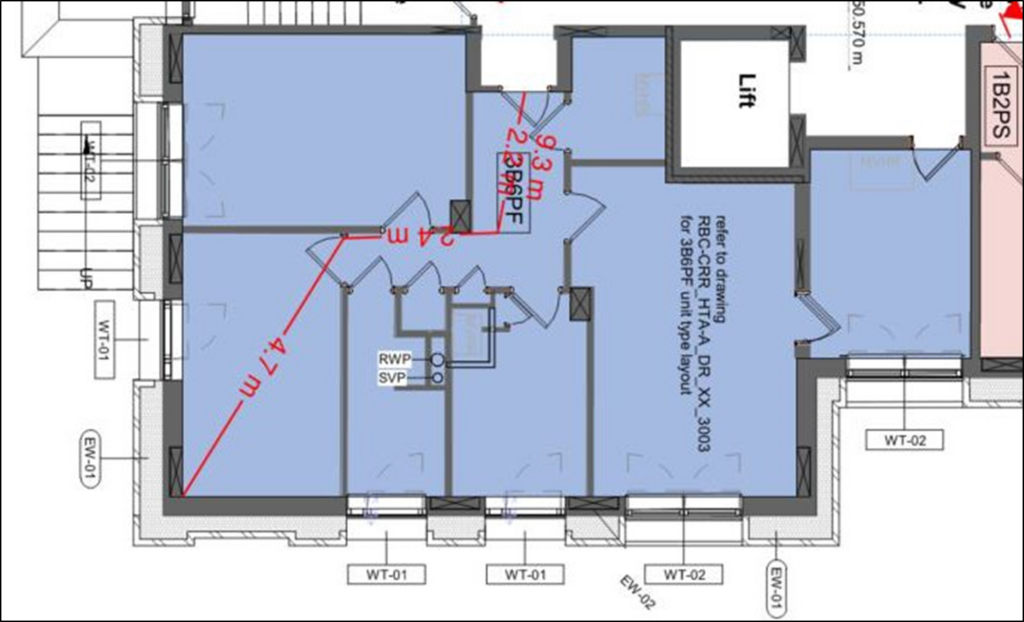
5.3.2
5.3.3 Common Residential Corridors
5.3.3.1 Levels 00
The general ground floor plan is indicated in Figure 5 below which indicates the routes of escape. The indicative travel distance from flat entrance doors to doors to a storey or final exit. . At the ground floor level there are two flats either side of the main entrance lobby, the flats are separated from the main entrance lobby by a short non- ventilated corridor. The non-ventilated corridor also provides direct access to the base of the escape stairs serving either side of the blocks.
AD B 2019 would require the residential corridor to be provide with smoke control to limit the passage of smoke from a fire in a flat on the ground floor entering and impacting on the escape stair. The smoke control would be in the form of a 1.5m2 shaft in line with the guidance in AD B section 3.50 – 3.53 or an equivalent mechanical system.
It would appear that the original building as designed in line with guidance in the CP3 Chapt. IV Part 1, the 1971 revision of the document makes no specific requirement for common residential corridors to be provided with ventilation so long as specific requirements, including separation of escape routes and ventilation of the stair cores were met, (refer to CP3 Ch IV Pt1 for full details), were met.
5.3.3.2 Upper Floors
Flats located on the upper levels of the building (Levels 01-15) are accessed by a central common corridor. The corridor has an escape door at either end, leading to an enclosed escape stair. The escape stairs are separated at the mid-point by an existing door and partition. The width of the separating door is to be confirmed.
The length of the corridor between doors to the stairs is approximately 20m. The cross-corridor door separating the stairs is located approximately 9.5m from one stair door and 10.5m from the other. Figure 66.3.2
On the upper floors the worst-case scenario of exit from a flat to either the stair door, or the cross-corridor door (whichever is the shorter distance) is approx.3.5m, as depicted on Figure 6.
It is recommended that the current protection to the stairs and the cross-corridor separation is discussed with the responsible person who will be completing the building FRA.
The doors and screens to the stair cores will be a minimum of FD 60S. The cross corridors separating the escape routes on the unvented corridor will be a minimum FD30S
The doors to the flats should be assessed to ensure that they will achieve a minimum FD30S.
These elements will be critical in maintaining the separation and control of smoke into the common escape areas as well as the escape stairs.
There does not appear to be any ventilation to the common corridor serving the blocks, it is noted that the travel distance from the flat entrance door to the stairs, or flat entrance door to the door separating escape routes is less than 4.5m and would appear to be in line with the guidance in CP 3 Chapter IV Part 1 clause 3.3.4. Dwellings with corridor approach where one dwelling or more is not provided an independent alternative route to a main stairway.
Current guidance recognises that smoke is likely to enter the common corridor on the floor of fire origin in the event that there is a fire in a flat, during the evacuation phase as well as during the firefighting phase. Where it is noted the distance within the corridor from apartment door to stair or separated part of corridor is short, this may still cause a risk to residents on the floor of fire origin and particularly those who may have a mobility or other impairment. Please also see section 5.2. The recommendation is that this is further reviewed by the responsible person as part of the building risk assessment.
It should be noted that for a building using current guidance this would not be acceptable and would require ventilation to both sections of corridor whether natural or mechanical to control smoke. To keep a smoke free corridor during evacuation and firefighting operation, but it is noted that this may not be practicable to retrospectively install in an existing block of flats.
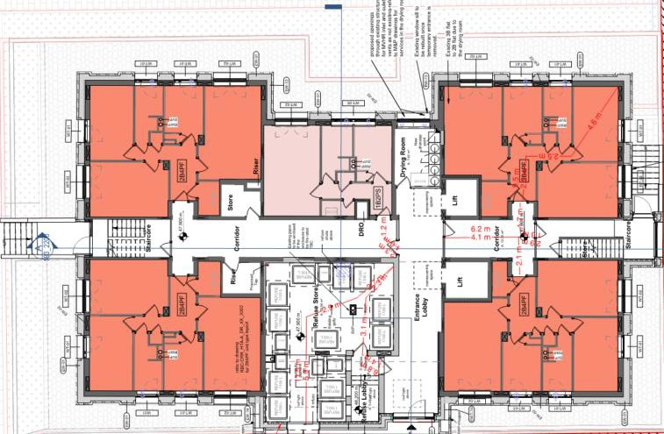
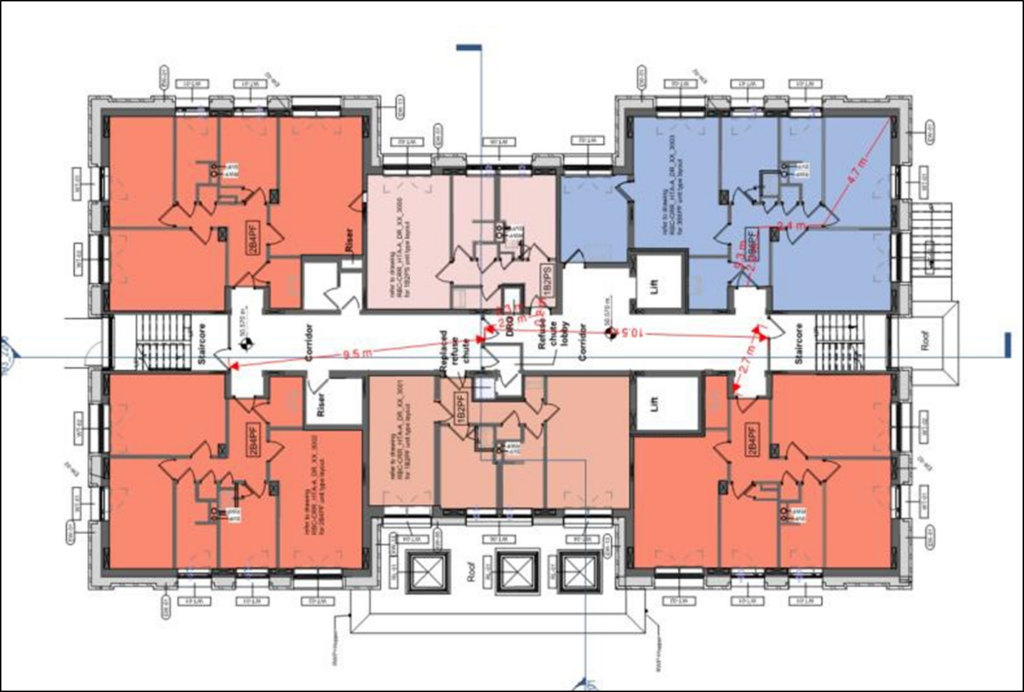
5.3.4 Residential ancillary areas
Within residential ancillary areas such as bin stores and plant rooms, travel distances should not exceed the following.
Area | Allowable Travel Distance within room | Allowable Travel Distance to nearest storey exit | ||
One-way | Multi-direction | One-way | Multi-direction | |
Bin stores, boiler rooms, transformer and switchgear rooms | 9m | 18m | 18m | 45m(1) |
Communal lounges and common amenity areas (including cycle store) | 18m | 45m(1) | 18m | 45m(1) |
Roof terraces and communal balconies | N/A | N/A | 45m | No limit |
Note 1: This may include up to 18 m with escape in one direction only |
Currently there are no extended travel distances within the ancillary areas as shown in Figure 7.
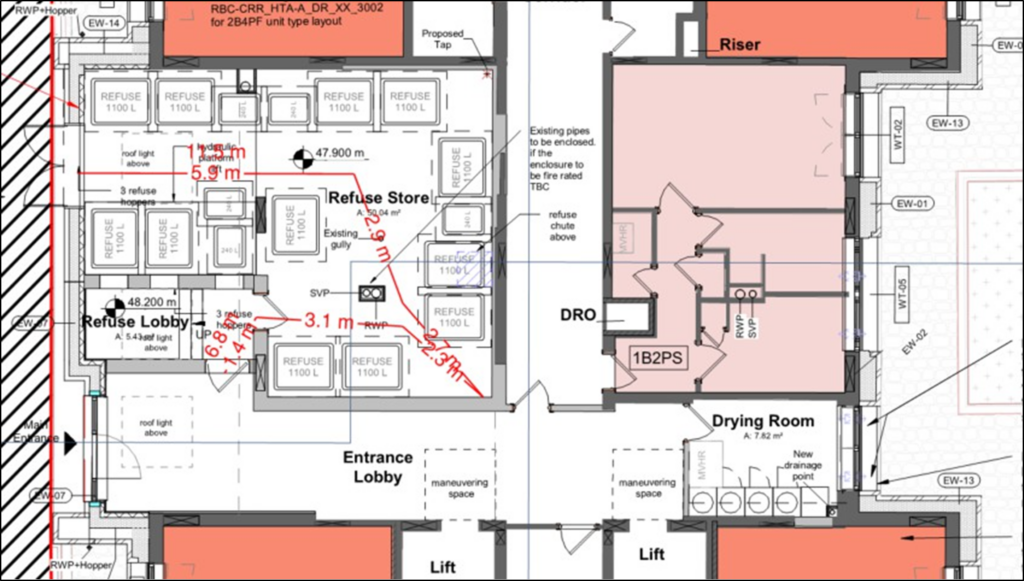
5.4 Vertical egress
5.4.1 Escape stair
The buildings are served by two stairs which provide escape from all residential floors and discharge at ground floor level, leading directly to outside.
The two stairs will also function as a fire-fighting access and thus under current guidance are to have a minimum clear width of 1100 mm. This width is for both means of escape and fire-fighting purposes.
It is noted that the stairs are existing and have a width of approximately 900mm and it would not be practicable for the width of the stairs to be altered to meet current guidance.
Reference should also be made to any requirements of Approved Document Part K and Part M where there may be additional requirements relating to the stairs.
5.4.2 Smoke control
At the time of construction the stairs would have been provided with an opening vent of 15ft2, approximately
1.4m2 at each landing level, and this would appear to have been altered at some time during past maintenance and would appear to now be a low level and high level vents with an opening area approximating to be in the region of 0.65m2.
Current guidance would require a minimum clear opening of 1.0m2 at each landing level or the highest point of the stair to limit the impact of smoke entering the stair on residents who may wish to escape. This figure is however based on the provision of smoke control within the common residential corridors limiting smoke entering the stairs.
The ventilation to the stairs will be remediated to provide a minimum 1.25m2 clear ventilation to all landing levels – the vents will be AOV’s on the top and bottom levels and will be manually operated on intermediate floors. The vents will be located at high level on each landing level. This has been agreed by Reading Borough Council Building control the building control body for the project.
5.4.3 Stair discharge
The residential staircase discharges to the outside directly at ground level as shown in Figure 9. Generally final exit should be no less than the width of the stair i.e., a minimum of 1100 mm, but it is noted as previous stated, this is an existing building and will be limited to existing situation.
It is noted that the south stair on the drawings has a store within the stair enclosure, it has been confirmed by RBC that the enclosure has been formed to prevent residents leaving items under the stairs. The area will not be used as a store and the door to this area will be a 30 minute fire resisting door and will be signed and kept locked shut at all times. The reference to store use will be removed from all drawings.
5.4.4 Protection of final exits
The protection of the final exit of both of the escape stairs should be in line with the current guidance in paragraph 3.68 and diagram 3.11 of AD B1.
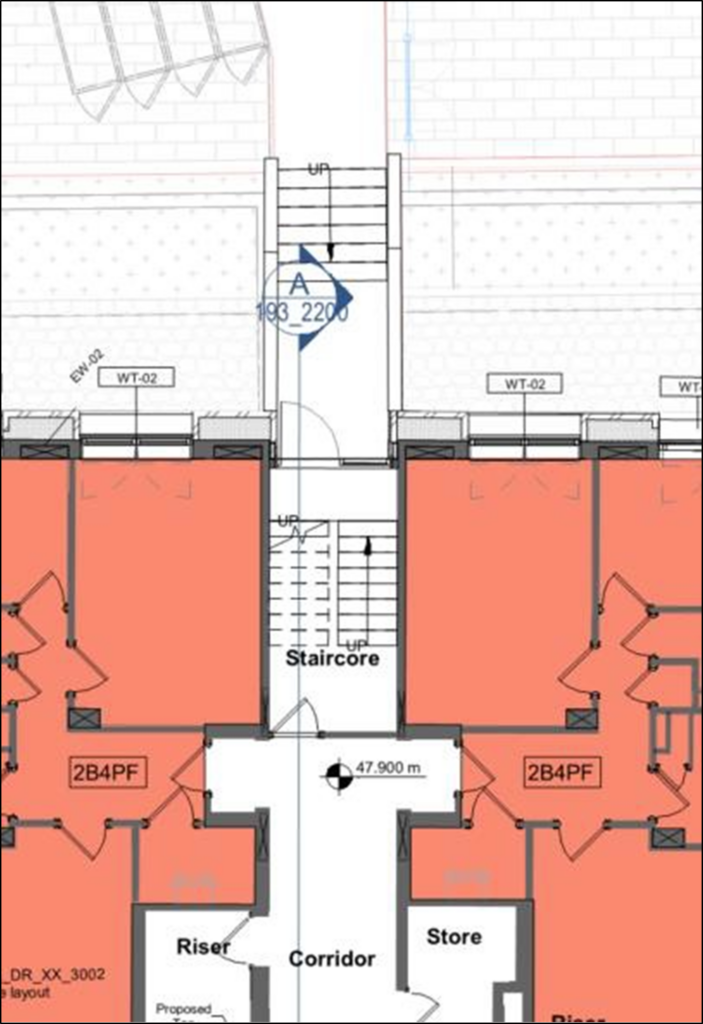
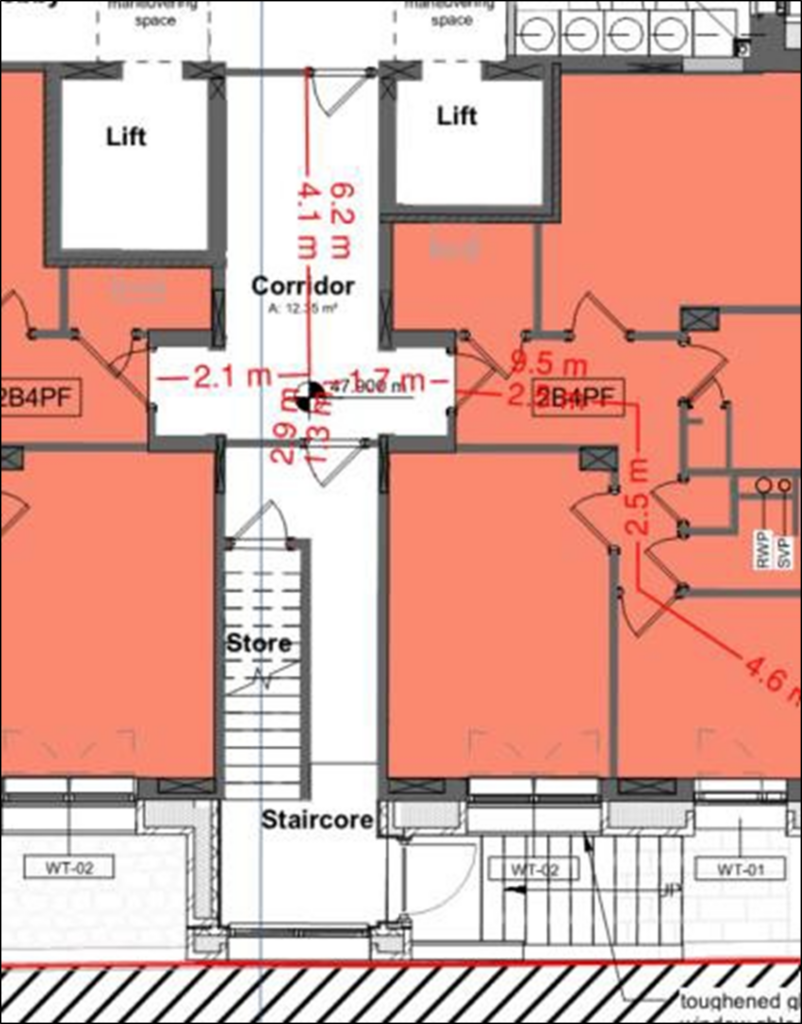
6 Active fire safety systems
6.1 Means of warning
6.1.1 Residential accommodation
As per current guidance the minimum acceptable fire alarm and detection system for the residential areas are summarised in Table 7.
Accommodation | Current System Category |
Open Plan Residential Apartments | LD3 – Grade D1(1) |
Residential Common Areas | L1 (2) |
Residential Plant / Ancillary Areas | L1(2) |
(1) Alarm systems should be designed and installed in accordance with BS 5839: Part 6. (2) Alarm systems should be designed and installed in accordance with BS 5839: Part 1. (Common corridors need detection only with no alarm – the alarm in the common areas is normally provided to activate smoke control systems) |
It is understood that the alarm and detection system within the flats is in line with the details in table 7 above.
It has been proposed by RBC that the existing AFD systems throughout the blocks are to be retained without alteration unless extended to cover new areas such as such as the new bin store areas.
It would appear that within the common corridor and stairs a common alarm system has been installed which includes sounders. At the time of the installation of the system a C&E matrix was developed between the designer/installer and RBC and is to be retained.
It is important that the actions to be taken by residents is carefully communicated in relation to a fire in a flat and the actions to be taken in the event of the activation of a detector/alarm in a common area to ensure that there is no conflicts/confusion between the different evacuation strategies.
It is recommended that the actions are regularly communicated to the residents/occupants of the building.
The details should also be reviewed by the person responsible for the building fire risk assessment and passed to the local fire service for their records.
6.2 Residential sprinkler system
The existing buildings would not have required a sprinkler system to be installed as part of the original construction guidance. However, under current guidance the buildings would require a sprinkler system to be installed.
It is noted that the three blocks have had a domestic sprinkler system installed in line with the guidance in BS9251- 2015. It is not known the category of the system installed or the date of commission and this should be confirmed by Reading Borough Council. It is understood that the system has been extended to the ancillary areas located at the ground floor and upper levels but not to the common residential corridor. The system commissioning details should be made available as part of the building safety information to aid maintenance, attending fire service in the event of an emergency and the responsible person who will be carrying out the building FRA under the RRO.
The details of the water supply and pumping systems should also be included in the sprinkler details. This is to be confirmed by Reading Borough Council.
6.3 Smoke ventilation systems
6.3.1 Refuse store
The lobby to the refuse store at Ground Floor should be provided with permanent ventilation. This would normally be 0.4 m2. It has been agreed by Reading Borough Council that the ventilation will be direct to the outside and they will not require ventilation to the lobby.
6.3.2 Residential common corridor and stair
Under current guidance the residential common corridors require smoke ventilation. It is also acknowledged that it may not be practicable to retrospectively install. It is noted that the building would appear to have met the guidance applicable at the time of construction, CP 3 Ch IV Pt 1 1960.
It is noted that each stair is provided with an opening vent with a free area of 1.0m2 opening at each landing level, the vent being located on an external wall, although at the time of construction it would appear that this would have been 15 ft2 (approx. 1.4m2) and may have been reduced at some time previous to the current works. To be confirmed by RBC.
It is noted that the original design guide would have not required this based on the building layout with 2 ventilated escape stairs, corridor separation and limited travel distance to escape stair or door separating corridor. Refer to 5.3.3.2 above.
6.3.3 Ground floor fire-fighting lobby
The fire-fighting lobby should be ventilated by a system to the same standard as the common corridors on the upper floors. This is to be reviewed as the design progresses.
6.4 Emergency lighting
Emergency lighting should be installed to provide temporary illumination in the event of failure of the primary power supplies to the normal lighting system. As part of the emergency lighting system, escape lighting will be provided to ensure the escape routes are illuminated at all times.
Emergency lighting should be installed in accordance with the recommendations of BS 5266-1:2016. It is understood that the emergency lighting will be installed as part of the current phase of refurbishment.
6.5 Fire safety signage
Fire safety signs will be installed where necessary to provide clear identification of fire precautions, fire equipment and means of escape in the event of fire. All parts of the development will be fitted with appropriate fire safety signage to comply with The Health and Safety (Signs and Signals) Regulations 1996, i.e., signage to be specified in accordance with BS 5499-4:2013, BS 5499-10:2014, and BS ISO 3864-1:2011.
It is understood that the signage will be installed as part of the current phase of refurbishment.
6.6 Emergency power supplies
Emergency power supplies are necessary for all active fire safety systems including the following:
- Automatic fire detection and alarm system;
- Sprinkler systems;
- Smoke control systems (fans, control equipment and AOVs);
- Firefighting provisions (fire main, lifts, lighting and communication); and,
- Emergency lighting (to be specified as the design progresses).
Secondary power supplies are recommended to be in accordance with BS 9991:2015 and BS 8219:2020.
Some systems (such as lighting and fire detection and alarm) may utilise local battery back-up instead of an emergency generator arrangement. Reading Borough Council/M&E consultant to confirm the proposed emergency power supplies to be provided.
7 B2 – Internal Fire Spread (linings)
When following the recommendations of AD B1 2019, the wall and ceiling linings within the Coley Park block refurbishment should comply with the recommendations of Table 5 below:
Location | European Class as described in BS EN 13501-1: 2018 |
---|---|
Small room of area not exceeding 4 m2 in a residential building and 30 m2 in a non-residential building | D-s3, d2 |
Other rooms | C-s3, d2 |
Other circulation spaces including the common areas of flats | B-s3, d2 |
8 B3 – Internal Fire Spread (structure)
8.1 Structural fire protection
As stated preciously the blocks are existing blocks constructed circa 1960. It is understood that there has been a recent structural report prepared for the blocks and it is requested that an indicative structural fire performance rating based on the findings of the reports is provided by the appointed structural engineer. For the purpose of this strategy the structural fire protection has been taken to be in line with the current AD B 2019.
The top storey height is more than 30 m, therefore the structural fire resistance for the building should achieve a minimum 120 minutes in line with recommendations in current guidance, AD B 2019, it is noted that the building is an existing structure and it may not be practicable to improve the current structural rating.
Elements of structure that only support a roof do not generally require fire resistance. The structure is considered to support more than only a roof if it supports a load other than the roof itself (e.g., rooftop plant requiring regular maintenance), or is essential to the stability of a compartment or other fire-resisting wall (internal or external) or performs as a floor and should be provided with fire protection.
It is understood that a previous structural reviews have been carried out for the blocks, by GBG report 4326 27th October 2017, RS Specialist services Ref: 21021/1 6th May 2021 and WFBA Project No. 19195D May 2021, however this did not appear to be specific in relation to structural fire resistance.
For complete information the recommendation is that the structural consultant provides and analysis of the likely structural fire resistance of the blocks.
8.2 Compartmentation
Table 6 summarises the compartmentation and fire-resistant construction requirements for all building elements which should achieve a fire resistance rating, as per current guidance. Refer to Appendix A for indicative compartmentation and fire-resistant construction drawings.
Every floor in the building should form a compartment floor with a fire resistance equivalent to that of the elements of structure for that building and include REI.
Residential apartments shall be separated by 60 minutes compartment walls, unless they are elements of the structure.
Elements requiring separation | Required Period of Fire Resistance (minutes) Refer to table B3 AD B for REI requirements |
---|---|
Protected entrance halls flats | 30 |
Flat entrance doors | FD30S |
Fire-fighting stairs | 60S (see section 5.3) |
Fire-fighting lift shafts* | 120 |
Fire service access / final exit routes | 60 (see section 3) |
Any area containing life safety equipment / diverse routes, including primary and secondary switch rooms* | 120 |
Compartment floors | 120 |
Other lift shafts | 120 |
Risers / protected shafts | 120 |
Common corridors | 60 |
Walls between adjacent flats | 60 |
Walls between flats and common corridors | 60 |
Plant rooms | 60 |
Refuse stores | 60 |
Cycle stores | 30 |
Storerooms | 30 |
Protected lobbies between final exit routes and accommodation | 30 |
Substation (to UKPN Standards) located external of the blocks in front of Block 205. | 240 |
Note: The original design code would have referred to Fire Lifts and confirmation is required from RBC as to whether these are still present and maintained safe for use by the fire service.
8.3 Fire doors
Fire doors should be provided as part of all fire resisting and compartment enclosures. The table below is a summary of the fire door rating recommendations.
FD XXS classification, the ‘XX’ corresponds to the period of fire resistance rating and ‘S’ denotes the recommendation for smoke seals. The FD XXS classification is achieved when tested to BS 476-22 or BS EN 1634-1. Vents into smoke shafts should achieve 60 minutes and a leakage rate no greater than 360 m3/h/m2 when tested in accordance with BS EN 1366-2.
Door Position | Rating (minutes)(1) |
---|---|
Apartment entrance doors | FD30S |
Protected entrance halls in flats | FD20 |
Protected stair / Firefighting stair doors | FD60S |
Passenger / Fire-fighting / Evacuation Lift doors | FD60 |
Protected lobby doors | FD30S |
Service riser doors | Half the rating of the wall for which it sits within (2) |
Compartment wall | Same rating as the wall for which it sits within (integrity only and smoke sealed) |
Plant and ancillary accommodation | Same rating as the wall for which it sits within (integrity only and smoke sealed) |
(1) All doors should be fitted with self-closing devices except for fire doors to cupboards and to service risers which are normally kept locked shut. (2) Where these are onto escape routes, smoke seals should be provided. |
As with previous comments within this strategy it is noted that the building is an existing structure, the original doors within the building would not have been provided with cold smoke seals or intumescent strips. It is understood from discussion with RBC that a survey has been completed for all doors within the blocks.
The recommendation is that the survey findings are reviewed in line with the table 7 above and be considered by the responsible person who carried out the building fire risk assessment.
8.4 Concealed spaces
Cavity barriers are provided to control and limit the risk of the unseen spread of fire and smoke within concealed cavities.
Cavity barriers must be provided to subdivide:
- Cavities which could otherwise form a pathway around a fire-separating element and closing the edges of cavities to reduce the potential for unseen fire and smoke spread; and
- Extensive cavities
- This recommendation is not relevant for the residential accommodation due to affording a high degree of compartmentation in which subdivision occurs at minimal lengths and does not exceed the lengths of which they are necessary in accordance with the guidance in AD B.
- This recommendation is not relevant for the residential accommodation due to affording a high degree of compartmentation in which subdivision occurs at minimal lengths and does not exceed the lengths of which they are necessary in accordance with the guidance in AD B.
8.5 Cavity barriers
The provision of cavity barriers should be made in accordance with the guidance in 5.16 and Diagram 5.3 of AD B (external walls). This includes:
- Around the edges of any opening (e.g. doors, windows and service penetrations);
- To close the edges of any cavities;
- At the top of the cavity; and
- In the continuation of compartment walls and compartment floors. (See 8,6 below).
In addition to this, taking guidance from AD B 2019 for cavity barrier requirements to sub-divide extensive cavities so that the distance between cavity barriers does not exceed the dimensions tabulated as follows.
Location of cavity | European Class of surface/product exposed in cavity (1) | Maximum dimensions in any direction (m) |
Between roof and ceiling | Any | 20 |
Any other cavity e.g. floor plenums, ceiling voids etc. | Class A1 Class A2-s3, d2 Class B-s3, d2 Class C-s3, d2 | 20 |
Not any of the above Classes | 10 | |
(1) Refer to Section AD B 2019 for test method details for each of the classifications |
Cavity barriers in a stud wall or partition, or provided around openings, may be formed of;
- Steel >0.5mm thick;
- Timber >38mm thick;
- Polythene-sleeved mineral wool, or mineral wool slab, in either case under compression when installed in the cavity; or
- Calcium silicate, cement-based or gypsum-based boards at least 12mm thick.
Cavity barriers provided around openings may be formed by the window or door frame if the frame is constructed of steel or timber of the minimum thickness listed in a) and b) above.
8.6 Fire-stopping at junctions
Fire stopping is required to maintain compartmentation at junctions between two internal compartment lines and between a compartment line and the building envelope and at openings or penetrations for services. Fire stopping is intended to close the relatively small openings at those junctions and prevent fire and smoke from bypassing the compartmentation via those openings.
The performance requirements are outlined as follows:
- For compartmentation to be effective there should be continuity at the junctions of the fire resisting elements enclosing a compartment and any openings from one compartment to another should not present a weakness.
- Where a compartment wall or compartment floor meets another compartment wall or an external wall, the junction should maintain the fire resistance of the compartmentation. Compartment walls should be able to accommodate the predicted deflection of the floor above by either:
- A suitable head detail between the wall and the floor, that can deform but maintain integrity when exposed to a fire, or;
- The wall may be designed to resist the additional vertical load from the floor above as it sags under fire conditions and thus maintain integrity.
- At the junction of a compartment floor with an external wall that has no fire resistance (such as a curtain wall) the external wall should be restrained at floor level to reduce the movement of the wall away from the floor when exposed to fire.
As fire stopping is a continuation of the compartment wall or slab, the performance should be in line with the compartment line it is associated with in terms of integrity and insulation for fire stopping. The fire stopping specification should ensure that products are tested and certified (via third party accreditation) to either BS 476-22 or BS EN 1364-4. Note that any chosen fire stopping product must be tested and certified in line with the intended application wherever possible (standard details), alternatively an engineering judgement can be made through advice given from a UKAS accredited body (non-standard details).
8.7 Fire-stopping around services
All openings for pipes, conduits or cables to pass through any part of a fire separating element should be:
- Kept as few in number as possible; and;
- Kept as small as practicable; and
- Fire stopped (which in the case of a pipe or duct should allow thermal movement).
The fire stopping of these must achieve at least the same fire rating performance of the fire separating elements it passes through.
Any passive or active fire stopping detail requires to be tested and certified in line with the intended application wherever possible (standard details), alternatively an engineering judgement can be made through advice given from a UKAS accredited body (non-standard details).
8.7.1 Pipes
Pipes which pass through fire separating elements (unless it is within a protected shaft), should meet either of the following provisions;
- Proprietary seals – Provide a proprietary sealing system.
- Restricted pipe diameter –
a. Where a proprietary sealing system is not used, fire stopping may be used around the pipe, keeping the opening as small as possible. The nominal internal diameter of the pipe should not be more than the relevant dimension given in the table below.
b. A pipe of lead, aluminium alloy, fibre-cement or PVC, with a maximum nominal diameter of 160mm, may be used with a sleeving of non-combustible pipe as shown in Figure 30 of BS 9991.
Situation | Maximum Nominal Internal Diameter (mm) | ||
Non-combustible material (1) | Lead, aluminium, aluminium alloy, PVC (2), fire-cement | Any other material (3) | |
Structure (but not a wall separating buildings) enclosing a protected shaft which is not a stair or lift shaft | 160 | 110 | 40 |
Compartment wall or compartment floor between apartments | 160 | 160 (stack pipe) 110 (branch pipe) | 40 |
Any other situation | 160 | 40 | 40 |
(1) A non-combustible material (such as cast iron or steel) which if exposed to a temperature of 8000C, will not soften or fracture to the extent that flame or hot gas will pass through the wall of the pipe. (2) uPVC pipes conforming to BS 4514 and uPVC pipes conforming to BS 5255. (3) These diameters are only in relation to pipes forming part of an above-ground drainage system and enclosed as shown within Figure 29 of BS 9991. In other cases, the maximum diameters against situation 3) apply. |
8.7.2 Ductwork
Ductwork will commonly be used for day-to-day ventilation and as part of any permanent ventilation proposal to plant/ancillary/refuse lobbies.
Where ductwork penetrates fire resisting elements, it must be fire stopped appropriately using any one of the methods outlined below (where appropriate):
- Thermally actuated fire dampers – Placed within the thickness of the fire-resisting element for which it is passing and be securely fixed. It is also necessary to ensure that, in a fire, expansion of the ductwork would not push the fire damper through the structure. Fire dampers and their frames should meet the appropriate fire resistance period of no less than 60 minutes (E) for the specific application when tested in accordance with BS EN 1366-2 (classified under BS EN 13501-3) or BS ISO 10294-5 (classified under BS ISO 10294-2).
- Fire resisting enclosures – Creating a protected shaft (housing the ductwork) passing through fire resisting elements.
- Fire rated ductwork – Creating a self-contained enclosure passing through a fire-resisting element. Fire resisting ductwork should meet the appropriate fire resistance period for the specific application when tested in accordance with BS EN 1366-1 and classified in accordance with BS EN 13501-3.
- Automatically actuated fire/smoke dampers – Placed within the thickness of the fire-resisting element for which it is passing and be securely fixed. It is also necessary to ensure that, in a fire, expansion of the ductwork would not push the fire damper through the structure. Fire dampers and their frames should meet the appropriate fire resistance period of no less than 60 minutes (ES) for the specific application when tested in accordance with BS EN 1366-2 (classified under BS EN 13501-3) or BS ISO 10294-5 (classified under BS ISO 10294-2).
The following exceptions are however should be noted:
- Kitchen extract ductwork – Method 2 and 3 are appropriate only.
- Ductworks passing through escape routes – Methods 2, 3 and 4 are appropriate only.
- Mechanical smoke shafts – Appropriate methods used should adhere to the design guide of smoke control mechanical ventilation systems as per BS EN 12101-6.
The proposed ventilation ducts/systems within the individual flats may need to consider the requirements of 8.7.3 as the systems are developed.
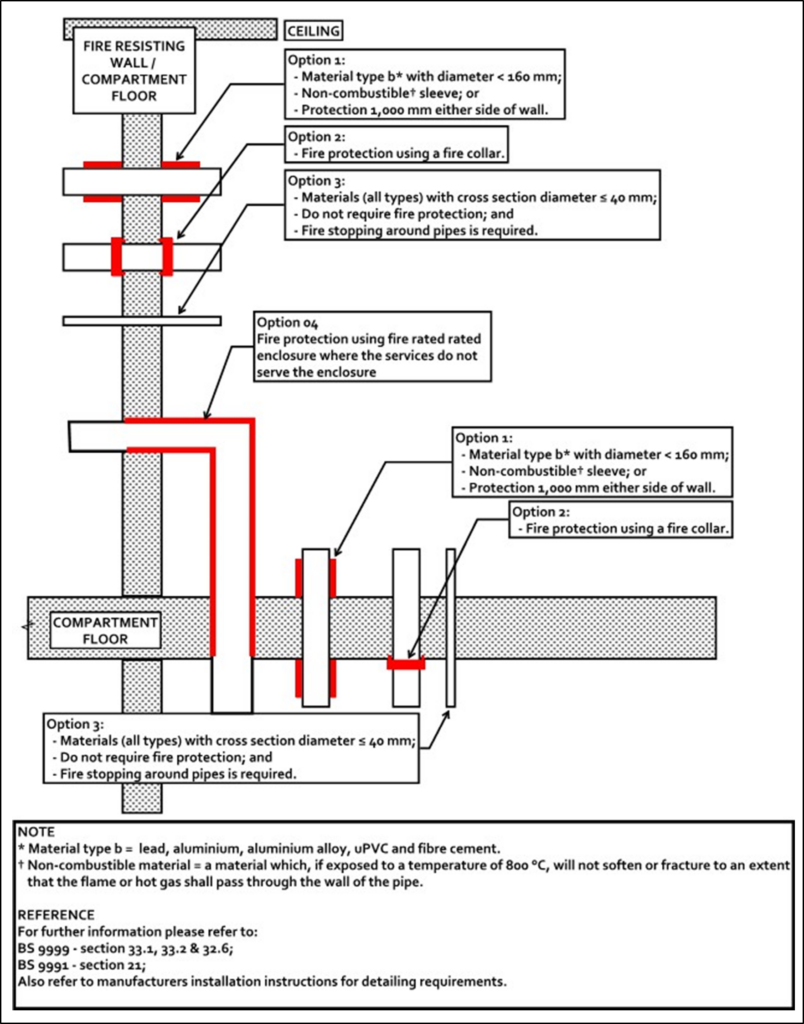
9 B4 – External Fire Spread
9.1 External wall construction
It is understood that the bulk of the proposed works to be carried out to the residential blocks at Wensley Road is in relation to the improvements to the external walls and in particular in relation to the replacement of the existing insulated render system understood to have been installed circa 1990.
The external wall of a building should not provide a medium for fire spread if that is likely to be a risk to life safety. Combustible materials and cavities in external walls and attachments to them can present such a risk, particularly in tall buildings.
It is noted that part of the proposed works will be the removal and replacement of the existing external wall system, which is understood to be rendered expanded polystyrene, (EPS), insulation over the existing Wimpey cast in-situ ‘no fines’ walls.
The replacement external insulation system will required to meet the guidance in AD B 1 2019 and Regulation 7 below.
Regulation 7(1)(a) requires that materials used in building work are appropriate for the circumstances in which they are used. Regulation 7(2) sets requirements in respect of external walls and specified attachments in ‘relevant buildings’.
Regulation 7(3) also provides permitted exemptions for certain components in the external and some specified attachments and should be referred to as part of the design and approval process.
As the building is greater than 18m it is considered a “relevant building”. Materials which become part of an external wall, or specified attachment, are to be of European Classification A2-s1, d0 or Class A1 in accordance with BS EN 13501-1:2018 to comply with Regulation 7, i.e. non-combustible material to the external façade. It is noted that commercial areas would also need to comply with Regulation 7.
The current proposals are that the new external wall insulation system will be a mineral based system and will meet the requirement of current guidelines.
9.2 Roof coverings
All roofs should be designated as BROOF(t4) in accordance with BS EN 13501-5.
It is understood that the existing roof is formed by a cast concrete deck. The existing roof covering is to be removed and replaced with a new and thicker inert insulation system and an ‘Alwitra’ single ply roofing system.
9.3 Space separation calculations
Unprotected areas (UPA) calculations have not been carried out as part of this retrospective strategy. It is understood that the openings within the external façade and relevant boundary distances are to be unaltered and therefore the existing UPA’s will remain. It is assumed that at the time of construction, that the unprotected areas within the façade were in accordance with the guidance.
10 Access and Facilities for the Fire Service
10.1 Vehicle access
Vehicle access to the various blocks will be via the Wensley Road perimeter road as shown in the block plan in Figure 10. The entrance point to the fire-fighting shaft and dry riser inlet should be within 18 m and in sight of the nearest parking location for the pumping appliance. It is noted that these are existing, and any proposed works should not make the current access provisions worse than they were prior to the works commencing.
The guidance at the time of constriction would have required the fire-fighting appliance to be able to be ‘brought to a reserved position within 60ft, (18m), of and in sight of the inlets to any rising mains.
The fire vehicle access routes should meet the recommendations shown in Table 10. Which is approximately in line with the guidance applicable at the time of construction.
The vehicle access point should be maintained clear at all times and where there is the possibility that the location could be blocked by other vehicles the recommendation would be that the area is clearly marked.
For the non-residential parts of the building, the route for laying fire hoses should meet the 60m limit from the fire engine to the furthest part of the non-residential area, in line with recommendations in AD B (see Figure 10).
10.2 Firefighting shaft
The current guidance for new build developments of this height, notes the following should be provided. Fire- fighting shafts should be provided to all residential buildings which are greater than 18m in height. In accordance with the recommendations of AD B & BS 9999, these fire-fighting shafts should be:
- Enclosed in 120 minutes fire-resisting construction with FD 60S fire doors;
- Provided with a fire-fighting stair having a minimum clear width of 1100 mm;
- Provided with an AOV at the head of the stair having a minimum free area of 1.0 m2;
- Served by a ventilated fire-fighting lobby on all upper levels and where specified in Section 6.3;
- Provided with a fire-fighting lift designed and installed in accordance with the BS EN 81-72: 2020. The landing doors of the fire-fighting lift should be no further from the stair door than 7.5m; and,
- Provided with fire mains having outlets on all levels located within the enclosure of the fire-fighting stair. Fire mains should be designed and installed in accordance with BS 9990:2015.
As the building is greater than this 18 m and less than 50 m in height, a dry rising fire main should be installed as a minimum as per AD B.
The guidance at the time of construction does not appear to be specific in relation to the construction of fire shafts but would appear to be covered in the guidance for fire lifts required a switch for passenger lifts to allow exclusive use by the fire service.
It is noted that there are 2 lifts that provide access to the upper floors of the blocks. The lifts provide access to alternate floors, odd and evens. The lifts have a fire service switch to allow fire service control. It is unknown if this has been maintained and whether the supply to the lifts has been altered since original construction. This is still to be confirmed by RBC.
It maybe that an upgrade of the lifts, if required, maybe unpracticable for the project in which case this will need to be discussed with RBC building control and the RBRFS for their approval as part of the statutory consultation process.
It is noted that the width of the existing stairs is approximately 900mm and it would not be considered practicable or realistic for this to be altered.
The guidance suggested that a fire lift “should not be more than 15ft (4.5m), from a main staircase, if it is the only staircase to which there is access, or about 50ft, (15m), if there is another staircase on the same floor to which there is access. In addition, if a fire lift is not in the main staircase enclosure or within 15ft of a door in the main staircase enclosure it should be within 15ft of a smoke stop door across a smoke stop door that leads to the main staircase”. The recommendation would be that the responsible person should review the doors under the RRO to ensure that they are satisfied that all relevant doors will be capable of resisting smoke, cold and hot, and fire. It may be suitable for this to be carried out by an FDIS approved company.
10.3 Dry rising main
The dry rising main within the existing blocks is unusual in its location, at Ground Floor level the inlet to the mains is located inside of the ground floor entrance and within a residential corridor.
CP 3 Chapter IV Part 1 required the inlet for the dry-rising main ‘to be placed in a convenient position on the external wall of the building and not more than 3ft above the level of the ground and they should be situated not more than 40ft away from the vertical position of the rising main. Inlets should be located in a glass fronted box’.
It is understood that previously the inlet for the dry-rising main was located on external of the blocks with the inlet being located in the ground with an access manhole. Historical access and obstruction issues led to the inlet being relocated within the ground floor corridor. It is understood that there has been communication between RBC and the Royal Berkshire Fire and Rescue service with regard to the location of the dry riser inlet who are in agreement. It is recommended that correspondence is readily available for review as part of the building fire safety information and for review by the responsible person as part of the building FRA under the RRO.
On the upper residential floors a dry rising main outlet is located at a central position within the common residential corridor. It is noted within the guidance at the time of construction that outlets for dry rising mains in section 704 (ii):
‘outlets from rising mains should be provided on every floor above the first in blocks of flats… They should be as near as possible to the main staircase or a fire lift’.
It is unclear if any of the lifts within the block are considered to be suitable for fire-fighting access and this should be confirmed by Reading Borough Council.
It is noted, that as the dry rising outlet is within the centre of the building, it is not located as near as possible to the staircases or lifts. Current guidance dictates that the dry riser outlet should be located within the protected enclosure of the fire-fighting stair, but noted that there is correspondence from the RBFRS accepting the location of the dry-riser outlets within the building however OFR would recommend that this is reviewed as part of the building risk assessment by the responsible person, and where not practicable the reasons are documented as part of the building fire safety information.
10.4 Hydrants
Hydrants should be provided within 90 m of an entry point to the building and not more than 90 m apart. The position of these should be confirmed by the design team. Existing hydrants can be within 100 m of an entry point to the building.
The buildings are existing and will be served by existing hydrants situated locally.
10.5 Wayfinding signage
To assist the fire service to identify each floor in a block of flats with a top storey more than 11 m above ground level, floor identification signs and flat indicator signs should be provided.
The stairs within the blocks have floor levels painted on the internal walls.
Appliance Type | Min. Width of Road between Kerbs | Min. Width of Gateways | Min. Turning Circle between Kerbs | Min. Turning Circle between Walls | Min. Clearance Height | Min. Carrying Capacity |
---|---|---|---|---|---|---|
Pump | 3.7m | 3.1m | 16.8m | 19.2m | 3.7m | 14 tonnes |
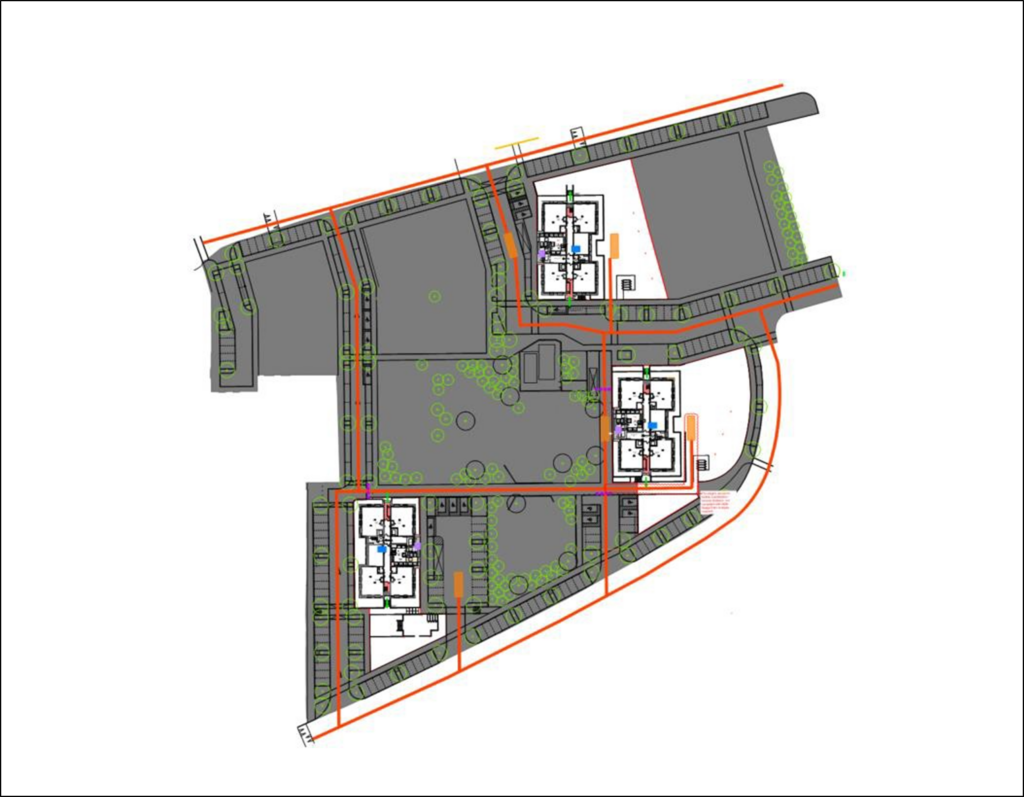
11 Management requirements
It is understood that Reading Borough Council do have a management plan for the blocks and that this will be reviewed as part of the development process during and after the completion of the refurbishment works.